Laser Welding: A Cutting-Edge Technology in Modern Industry
As we have seen, laser welding offers a number of significant advantages over traditional welding methods. Let's explore this innovative technology in more detail:
How does laser welding work?
The laser welding process is based on concentrating a large amount of energy into a very narrow laser beam. When this beam hits the material, the thermal energy generated melts the metal, creating a strong joint.
There are different types of lasers used in welding, each with its own characteristics:
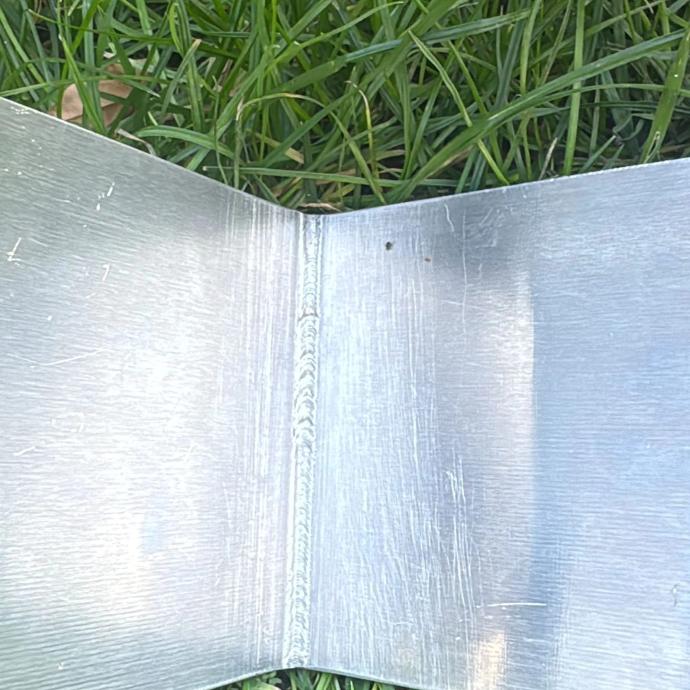
- Carbon dioxide (CO₂) lasers: The most common, they offer high power and are suitable for welding medium-thick materials.
- Fiber optic lasers: They allow precise beam focusing and are used for welding thin materials and complex components.
- Disc lasers: They offer very high power and are ideal for high-volume industrial applications.
Welding processes:
- Sudură prin conducție: The heat is conducted into the material, melting a relatively large area.
- Key welding: The laser beam penetrates the material, creating a V-shaped key.
- Hybrid welding: The combination of laser welding and another process, such as MIG/MAG, to improve performance.
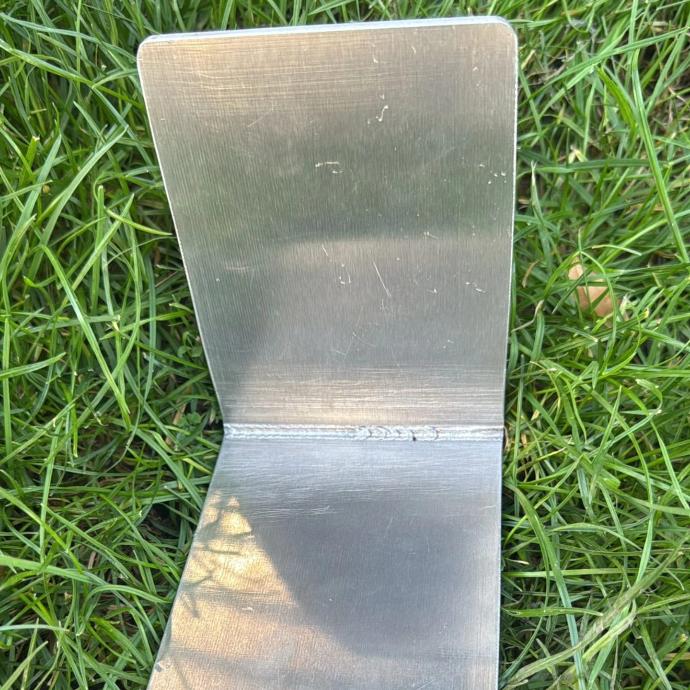
Additional advantages of laser welding
- Superior seam quality: The seams are extremely clean with minimal heat affected area, leading to increased mechanical strength and durability.
- Versatility: Can be used to weld a wide range of materials, including metals, alloys and some plastics.
- Accuracy and repeatability: The process is very precise and can be easily automated, leading to efficient and high-quality production.
- Cost reduction: Although the initial investment in equipment is high, per-unit costs can be lower due to the speed and efficiency of the process.
- Reduced environmental impact: Generates fewer emissions and waste compared to other welding processes.
Typical applications of laser welding
- Automotive industry: Welding of body components, batteries and exhaust systems.
- Electronics: Assembling integrated circuits, soldering miniature components.
- Aerospace: Manufacturing components for aircraft and missiles.
- Medical: Production of surgical instruments and implants.
- Energetic: Welding of components for wind turbines and solar panels.
The future of laser welding
Tehnologia de Laser Welding technology continues to develop rapidly,with new innovations emerging constantly. Current trends include:
- Equipment miniaturization: Lasers are becoming increasingly compact and easier to integrate into robotic systems.
- Increased power and speed: Allowing the welding of thicker materials and higher production rates.
- Integration with other technologies: Combination with vision systems and sensors for greater precision and flexibility.
In conclusion, laser welding is a cutting-edge technology that offers a number of significant advantages over traditional welding methods. As the technology continues to develop, laser welding is expected to play an increasingly important role in various industries.